Keyways play a crucial role in mechanical systems, enabling power transmission between shafts and other machine elements. Cutting an internal keyway can be a challenging task, but with the right method and tools, it can be done with precision and efficiency.
In this comprehensive guide, we will discuss seven popular internal keyway cutting methods. We will explore the advantages and limitations of each method, provide use case examples, and offer best practices to help you make an informed decision.
7 Methods for Cutting Internal Keyways
- Broaching
- Inserted broaching tools
- Driven broaching heads (Live broaching tools)
- Shaping / Slotting
- Keyseating
- Milling
- Wire-Cut EDM
1. Broaching
What you need
Machine: A Broaching machine
Tooling: Keyway Broaches
Introduction
Broaching is a widely used method for cutting internal keyways, involving the use of a broach—a specialized cutting tool with a series of progressively larger teeth. The broach is clamped on the broaching machine and either pulled or pushed through the workpiece to broach the keyway.
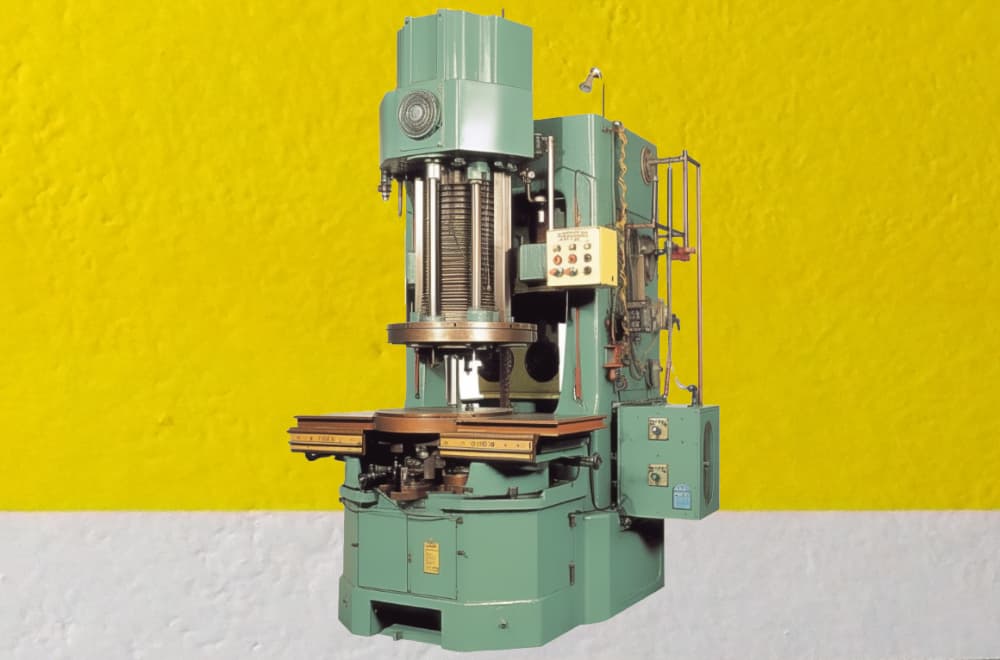
Advantages
- High precision and accuracy: Broaching can cut keyways with tight tolerances and excellent repeatability.
- Surface finish: The progressive cutting action of a broach results in a smooth surface finish.
- Suitable for high-volume production: Broaching is a fast and efficient method, making it ideal for mass production.
Limitations
- Expensive tooling and machinery: Broaching machines and custom broaches can be costly investments.
- No blind holes: The broach has to go through the workpiece for this method.
- The workpiece cannot be finished on one machine and needs to be reclamped. Because only the broaching operation can be done with this method.
- Limited to certain material types: Broaching is generally suited to softer materials and may struggle with harder or more abrasive materials.
- Less flexible due to custom tooling requirements: Broaches are designed for specific keyway geometries, making it difficult to accommodate design changes or multiple keyway profiles.
Use case examples
- Automotive industry: Transmission gears and components, such as synchromesh assemblies.
- Aerospace: Turbine engine components, including compressor and turbine disks.
- Heavy machinery: Gearboxes, shaft couplings, and power transmission components.
Best practices
- Ensure proper alignment of the broach and workpiece: Accurate alignment is crucial to avoid tool deflection and ensure consistent internal keyway dimensions.
- Use the correct broach size and type for the desired keyway geometry: Selecting the appropriate broach will ensure optimal cutting performance and extend tool life.
- Regularly inspect and maintain the broaching tool to prevent wear and damage: Keeping the cutting edges sharp and free of damage will improve cutting performance and extend tool life.
2. Keyway Cutting with Inserted Broaching Tools
What you need
Machine: One of the following: CNC Lathe, CNC Machining Center, Slotter Machine (Slotting Machine), Shaping Machine, Conventional Lathe, Milling Machine
Tooling: Keyway Cutting Insert, Insert Holder
Introduction to Inserted Broaching Tools
Cutting keyways with inserted broaching tools is a modern broaching method, using a tool holder with replaceable cutting inserts. These keyway cutting tools can be used on CNC machines and a variety of other machines for slotting and shaping. This offers greater flexibility and reduced tooling costs compared to traditional broaching.
Keyway cutting using this method on a CNC lathe or machining center eliminates the need to reclamp the tool on a separate machine in order to broach the keyway.
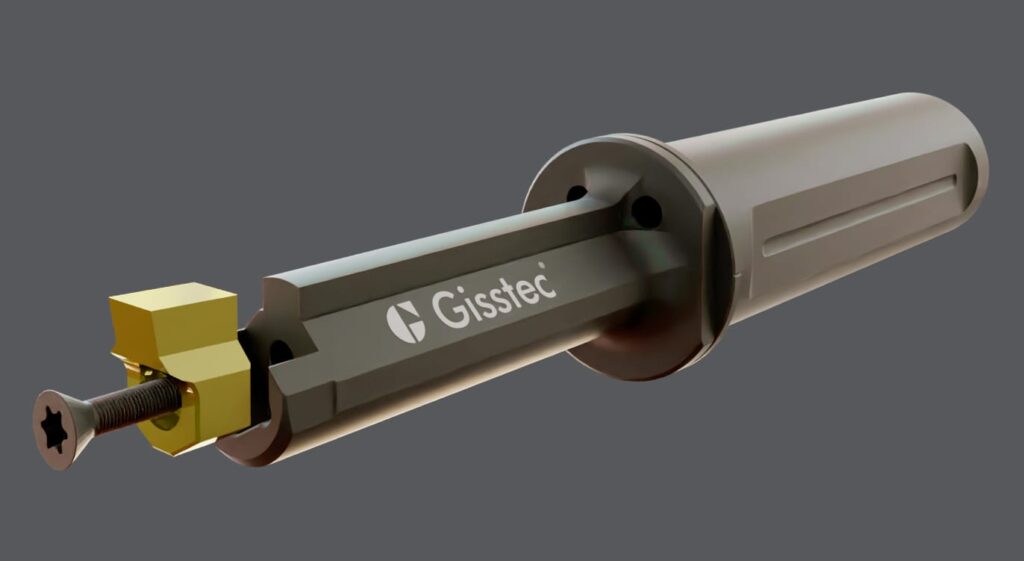
In this method, first the workpiece is clamped in position. Then the keyway is cut by the tool through a series of successive passes. The tool removes an equal amount of material with each pass until the required size of the keyway is achieved.
It’s also called static broaching tools since the Z-axis movement necessary for chip removal comes from the machine itself. On the other hand, a driven broaching unit generates the back-and-forth movement in Z-axis by itself. (See third method for details)
Advantages of Inserted Broaching Tools
- One of the lowest cost methods for cutting an internal keyway while maintaining excellent precision: The use of replaceable inserts eliminates the need for expensive custom broaches or specialized machines.
- Cuts keyways in blind holes: Allows for cutting keyways inside blind holes with or without a relief groove
- Enhanced flexibility with interchangeable inserts: Multiple keyway profiles and tolerances can be machined using a single tool holder and a variety of cutting inserts.
- Improved tool life and easier maintenance: Cutting inserts can be replaced when worn or damaged, extending the life of the tool holder and reducing maintenance costs.
- Cutting inserts can have their lifespan extended by resharpening them multiple times, allowing for their reuse.
- Works with a wide range of material types: Can be used to machine keyways in both soft and hard materials, including cast iron, steel, titanium and non-ferrous alloys.
Limitations
- Slower process compared to traditional broaching: Multiple passes are required to create the keyway. So, it’s more efficient overall for small batches.
- Less suitable for high-volume production: While inserted broaching tools offer greater flexibility, they are not as efficient as some of the other methods for large-scale production.
Use case examples
- Small-scale production: Gears, pulleys, and other components requiring precise keyways.
- Prototyping: Testing new keyway designs or validating component fit and function.
- Repair and maintenance: Retrofitting existing components with new keyways or correcting worn or damaged keyways.
Best practices
- Use the appropriate cutting insert for the material being machined: Different materials require specific cutting geometries and coatings for optimal performance and tool life.
- Ensure proper tool holder alignment with the workpiece: Accurate alignment is essential to maintain consistent keyway dimensions and prevent tool deflection. Use appropriate tools to correct any axis errors.
- Regularly inspect and replace worn cutting inserts: Timely replacement of cutting inserts will ensure optimal cutting performance, surface quality and extend tool life.
3. Keyway Cutting with Driven Broaching Heads
What you need
Machine: CNC Lathe with a C-axis or a CNC Machining Center
Tooling: Driven Broaching Unit
Introduction to Driven Broaching Tools
Driven broaching heads (live broaching units) are specialized tools that can be mounted on CNC lathes with C-axis or CNC milling machines. These driven tools convert the rotary motion from the turret/spindle to linear motion to drive an inserted broaching tool through the workpiece.
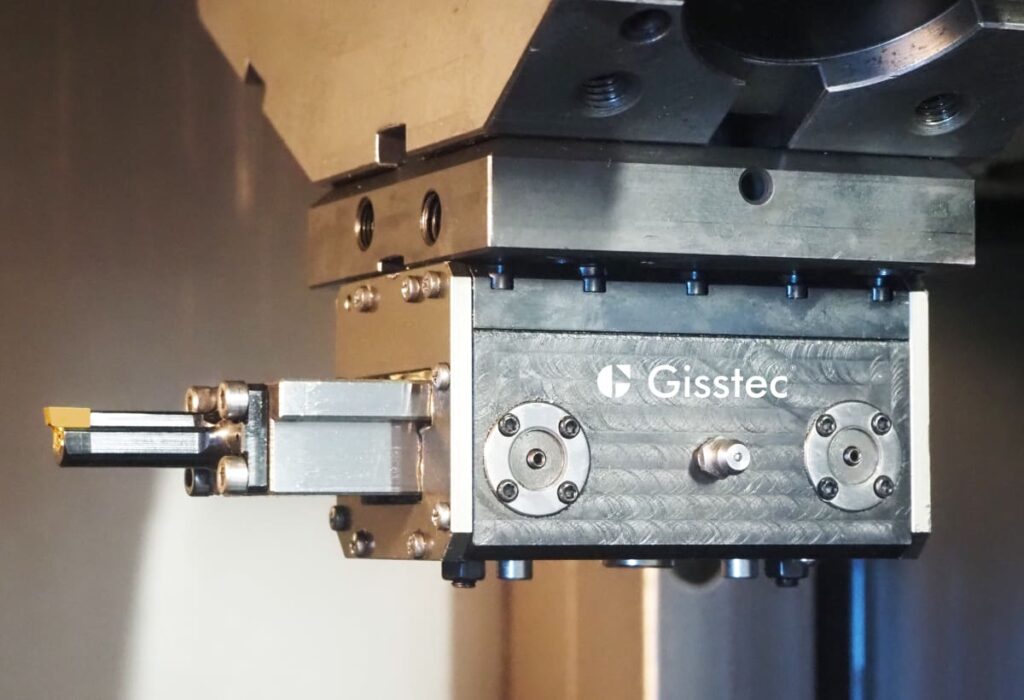
This high-speed broaching method is commonly used on CNC lathes. It creates keyways similarly to the second method, which utilizes static broaching tools. However, driven broaching tools are remarkably faster, exceeding the speed of static tools by over 10 times.
Advantages
- Fastest method without a dedicated keyway cutting machine: It enables the finishing of the workpiece without unclamping and setting it up on a separate machine.
- Enhanced flexibility: Driven broaching heads can be used with existing CNC equipment, eliminating the need for dedicated broaching machines.
- Cuts keyways in blind holes: Allows for cutting internal keyways in blind holes
- High precision and accuracy: Driven broaching heads can produce keyways with tight tolerances and excellent repeatability.
- Excellent choice for medium to large production volumes: Combines the efficiency of dedicated broaching machines with the convenience of finishing the operation on the same machine, streamlining your production process.
- Works with a wide range of material types: Can be used to machine keyways in both soft and hard materials, including cast iron, steel, titanium and non-ferrous alloys.
- Some driven broaching heads come with advanced error correction features, which allows for quick troubleshooting.
Limitations
- Although investing in a driven broaching tool can provide a rapid return on investment for larger production batches, it may not be the most cost-effective solution if you only occasionally require broaching operations.
- The size of the workpiece is limited to the capacity of the CNC lathe being used.
- Driven broaching heads have a limited stroke usually going up to around 65mm (~2.5”)
- Maximum keyway width is limited depending on the material, but is generally not larger than 16mm (~5/8”)
Use case examples
- Medium and large-scale production: Components such as gears, pulleys, and couplings requiring precise keyways.
- Leveraging existing CNC machines: Manufacturers looking to expand their keyway cutting capabilities without investing in dedicated broaching machines.
Best practices
- Use the correct broaching head and cutting tool for the desired keyway dimensions and material type: Selecting the appropriate tooling will ensure optimal cutting performance and extend tool life.
- Ensure proper alignment of the driven broaching head and workpiece: Accurate alignment is crucial to avoid tool deflection and maintain consistent keyway dimensions.
- Regularly inspect and maintain the cutting tool and broaching head to prevent wear and damage: Keeping the cutting edges sharp and free of damage will improve cutting performance and extend tool life.
4. Keyway Cutting by Shaping / Slotting
What you need
Machine: Shaping machine, Slotter/Slotting machine
Tools: Keyway cutting tools / Internal keyway cutter
Introduction to Shaping and Slotting
Shaping or slotting is a method that involves using a reciprocating single-point cutting tool to remove material and create the keyway. The cutting tool moves horizontally or vertically along the workpiece, gradually cutting the internal keyway with each pass.
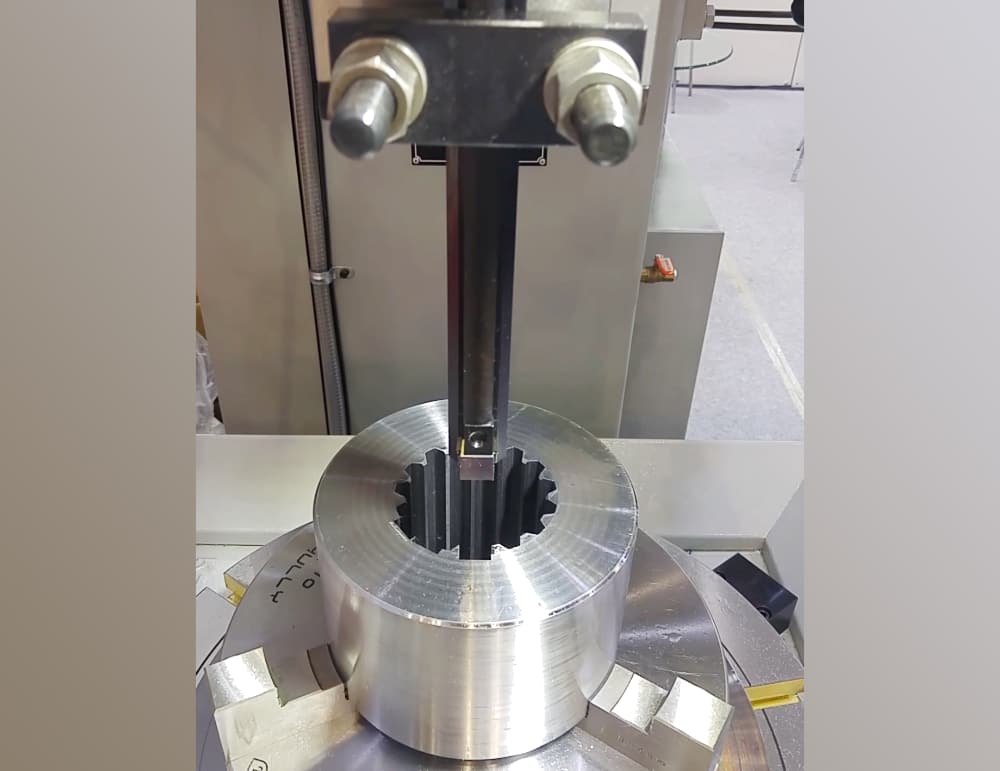
The operation is performed on dedicated machines such as a shaper or a slotter. As for cutting tools, either integral keyway cutting tools or inserted broaching tools as in the second method can be used. An adapter might be necessary to clamp the tools depending on the machine type.
Advantages of Shaping / Slotting
- Low tooling and machinery costs: Shaping machines and cutting tools are typically less expensive than dedicated broaching or keyseating equipment.
- Simple setup and operation: The shaping process is straightforward, making it accessible to operators with varying levels of experience.
- Cuts keyways in blind holes: Allows for cutting keyways inside blind holes
- Works with a wide range of material types: Shaping can be used to machine keyways in both soft and hard materials, including cast iron, steel, and non-ferrous alloys.
Limitations
- Limited precision and accuracy: Shaping may produce less accurate keyway dimensions and require more skill to achieve consistent results.
- Slower cutting process: The reciprocating motion of the shaping tool can be less efficient than the continuous cutting action of a broach or the electrical discharge process of Wire-Cut EDM.
- Poor surface finish compared to other methods: Shaping may produce rougher surface finishes, requiring secondary operations to achieve desired results.
Use case examples
- General engineering: Pulleys, sprockets, and couplings used in a variety of industries and applications.
- Low-volume production: Custom or unique components requiring keyways, where the expense of dedicated broaching or keyseating equipment is not justified.
- Educational institutions: Training and teaching purposes, where students can learn fundamental machining techniques and principles.
Best practices
- Use the appropriate shaping tool for the desired keyway dimensions: Selecting the correct cutting tool will ensure optimal performance and extend tool life.
- Ensure proper alignment of the shaping tool and workpiece: Accurate alignment is essential for maintaining consistent keyway dimensions and preventing tool deflection.
- Regularly inspect and maintain the cutting tool to prevent wear and damage: Keeping the cutting edges sharp and free of damage will improve cutting performance and extend tool life.
5. Milling Internal Keyways
What you need
Machine: CNC Machining Center, Milling Machine
Tooling: Angle head, cutting tool e.g. end mill
Introduction to Milling Keyways
Milling an internal keyway requires the cutting tool, e.g. an end mill to to cut at 90º along the bore length. This kind of operation will usually require an angle head to dive into the bore vertically. The keyway is machined by removing material with the rotating cutting tool which is clamped to the angle head.
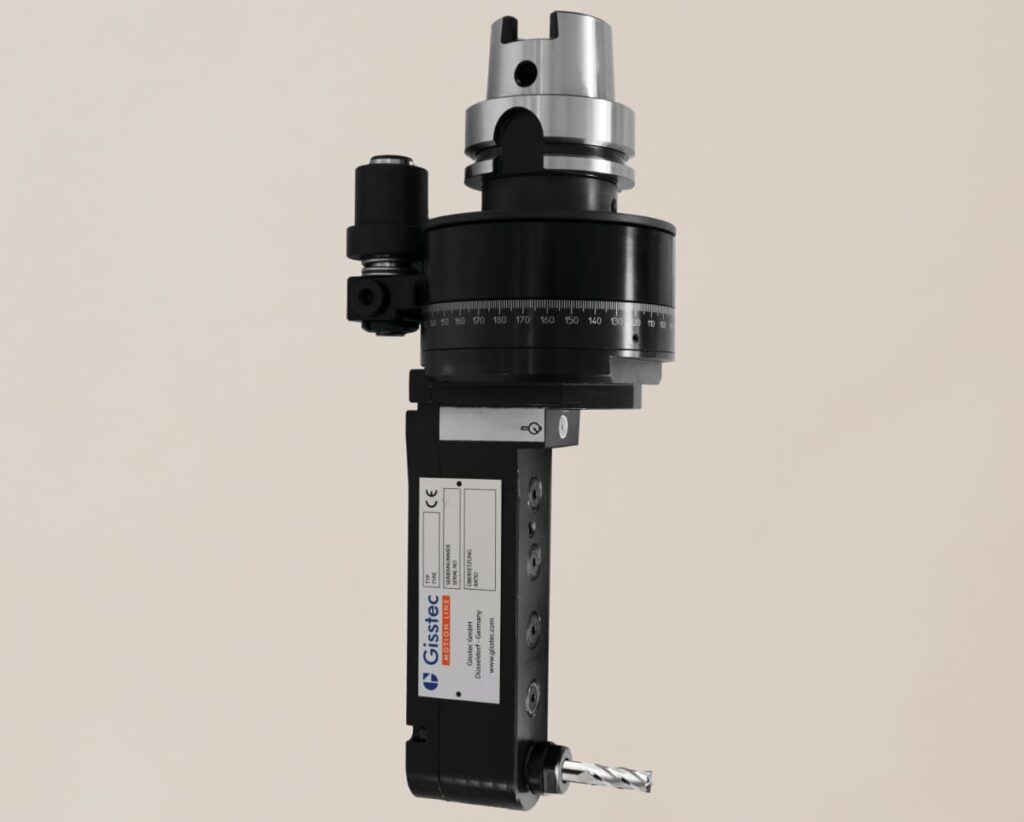
During the machining operation the lower body of the angle head needs to dive into the bore to cut the internal keyway. So this method is suited for workpieces with a bore large enough to accommodate the angle head.
This process can be performed on a variety of milling machines, including manual, CNC, and multi-axis machines.
Advantages of Milling an Internal Keyway
- Suitable for a wide range of material types: Milling can machine keyways in soft and hard materials, including cast iron, steel, and non-ferrous alloys.
- Can create keyways with varying depths and widths: Milling allows for greater control over keyway dimensions and can accommodate design changes more easily than dedicated broaching equipment.
- Compatible with CNC machines for automated and precise keyway cutting: Milling can be integrated into CNC machining processes, offering improved accuracy, repeatability, and efficiency.
- Can machine keyways in blind holes.
Limitations
- Requires specialized tooling for internal keyways: Milling an internal keyway often requires an angle head. So it might be more suitable for higher-value or higher-volume milling parts in order to justify the investment.
- Limited to certain keyway geometries: Milling may struggle with complex keyway profiles or non-standard shapes, particularly when using standard cutting tools.
- Slower process compared to broaching: Milling can be less efficient than dedicated broaching machines, especially for high-volume production.
Use case examples
- General engineering: Gears, sprockets, and couplings used in various industries and applications.
- Automotive industry: Transmission components, such as gears and shafts, requiring precise keyways for power transmission.
- Prototyping and small-scale production: Custom or unique components requiring keyways, where the flexibility of milling is advantageous over dedicated broaching equipment.
Best practices
- Use the appropriate milling cutter for the desired keyway dimensions and material type: Selecting the correct cutting tool will ensure optimal performance and extend tool life.
- Ensure proper alignment of the milling cutter and workpiece: Accurate alignment is essential for maintaining consistent keyway dimensions and preventing tool deflection.
- Regularly inspect and maintain the cutting tool to prevent wear and damage: Keeping the cutting edges sharp and free of damage will improve cutting performance and extend tool life.
6. Keyseating
What you need
Machine: A Keyseating Machine
Tooling: Keyseater Tools / Internal keyway cutter
Keyseating is a method that uses a reciprocating cutting tool, called a keyseater or keyway cutter, to cut the keyway. The cutting tool is mounted vertically in the machine and moves up and down while the workpiece remains stationary.
Advantages of Keyseating
- Low tooling and machinery costs: Keyseating machines and cutting tools are generally less expensive than dedicated broaching equipment.
- Suitable for large workpieces and deep keyways: Keyseating machines can accommodate larger components and create deeper keyways than many other methods.
- Works with a wide range of material types: Keyseating can be used to machine keyways in both soft and hard materials, including cast iron, steel, and non-ferrous alloys.
Limitations
- Slower cutting process: The reciprocating motion of the keyseater tool can be less efficient than the continuous cutting action of a broach or the high-speed cutting of a driven broaching head.
- Limited precision and surface finish: Keyseating may produce rougher surface finishes and less accurate keyway dimensions compared to broaching or Wire-Cut EDM.
- Requires skilled operators: Achieving consistent results with keyseating requires experience and skill, particularly when working with harder materials or complex keyway profiles.
Use case examples
- Large-scale components: Industrial gearboxes, couplings, and other power transmission elements in heavy machinery.
- Shipbuilding: Propeller shaft keyways and components for marine propulsion systems.
- Power generation: Turbine and generator shaft keyways in hydroelectric, nuclear, and fossil fuel power plants.
Best practices
- Use the correct keyseater tool for the desired keyway dimensions: Selecting the appropriate cutting tool will ensure optimal performance and extend tool life.
- Ensure proper alignment of the keyseater and workpiece: Accurate alignment is essential for maintaining consistent keyway dimensions and preventing tool deflection.
- Regularly inspect and maintain the cutting tool to prevent wear and damage: Keeping the cutting edges sharp and free of damage will improve cutting performance and extend tool life.
7. Cutting Keyways with Wire-Cut EDM
What you need
Machine: Wire EDM
Introduction to Wire-Cut EDM Keyway Cutting
Wire-Cut EDM (Electrical Discharge Machining) is a process of cutting electrically conductive materials with high precision. It uses a thin, electrically charged wire to cut the required keyway by eroding material via electrical discharge.
This process is highly accurate and can be used to machine intricate keyway profiles in conductive materials. In addition, it is particularly effective in cutting precise keyways when working with hard materials.
Advantages of Wire-Cut EDM
- High precision and accuracy: Wire-Cut EDM can produce keyways with tight tolerances and excellent repeatability, making it ideal for high-precision applications.
- No mechanical forces exerted on the workpiece: The non-contact cutting process eliminates the risk of tool deflection or workpiece distortion.
- Can cut hard materials and complex geometries: Wire-Cut EDM can machine keyways in hardened materials, such as tool steels, and create intricate profiles that may be difficult or impossible with other methods.
- Excellent surface finish: The controlled electrical discharge process results in a smooth surface finish, often eliminating the need for secondary operations.
Limitations
- Slower process compared to other methods: Wire-Cut EDM can be time-consuming, particularly for deep keyways or large workpieces.
- Higher operational costs: Wire-Cut EDM machines and consumables, such as wire and dielectric fluid, can be expensive.
- Only suitable for electrically conductive materials: Non-conductive materials, such as ceramics or certain polymers, cannot be machined using Wire-Cut EDM.
Use case examples
- Machining hardened materials: Tool and die manufacturing, where keyways must be cut in hardened materials or components.
- Complex geometries: Intricate keyway profiles and shapes, such as non-standard or curved keyways, that cannot be machined using conventional methods.
Best practices
- Use the appropriate wire type and size for the material being machined: Wire selection is critical to achieving optimal cutting performance and minimizing wire breakage or wear.
- Ensure proper alignment of the wire and workpiece: Accurate alignment is essential to maintain consistent keyway dimensions and prevent wire deflection.
- Regularly maintain and clean the Wire-Cut EDM machine to ensure optimal performance: Timely maintenance, such as replacing worn wire guides or cleaning the dielectric fluid system, is crucial to the overall efficiency and longevity of the machine.
Conclusion
Cutting internal keyways is an essential task in many industries, and selecting the most appropriate method for a particular application is critical to achieving the desired results efficiently.
Broaching, keyway cutting with inserted broaching tools, keyseating, Wire-Cut EDM, shaping, milling, and keyway cutting with driven broaching heads each offer unique advantages and limitations.
The ultimate choice will depend on the size and geometry of the workpiece, keyway dimensions and quantity. By understanding these factors and applying best practices, manufacturers can make informed decisions and optimize their keyway cutting processes to maximize efficiency, precision, and overall performance.