Whether you’re machining on a 3 or 4-axis CNC machining center or a state-of-the-art 5-axis machining center, angle heads come to rescue for machining a variety of workpieces.
In the world of CNC (Computer Numerical Control) machining, the addition of angle heads significantly streamlines the manufacturing process. Let’s take a straightforward, practical look at the different types of angle heads and how they’re used in everyday machining.
We’ll look into 6 common types of angle heads for machining centers:
- Right Angle Heads
- Adjustable Angle Heads
- Slim Angle Heads
- Double Output Angle Heads
- Heavy-Duty Angle Heads
- Modular Angle Heads
1. Right Angle Heads
A right angle head, as the name suggests, is positioned at a 90-degree angle. This handy design lets you work on the side surfaces of a piece without needing to move it around.
Imagine you’re machining a workpiece on a 3-axis CNC machining center and want to drill holes into the sides. Without a right angle head, you’d have to rotate the workpiece for each side—quite a hassle, right? The right angle head lets you drill those holes easily, without all the fuss.
Whether you’re manufacturing parts for Benz or Airbus, it’s a popular angle head across various industries, from automotive to aerospace.
2. Adjustable Angle Heads
Sometimes, the machining task in hand requires more flexibility. Enter adjustable angle heads. With the ability to set them at any desired angle, these tilting heads are like the ‘Swiss Army knife’ of CNC machining.
Take the aerospace industry, for example. The parts often have complex shapes that need precise machining at various angles. Adjustable angle heads are ideal for this task, providing the flexibility needed for such detailed work.
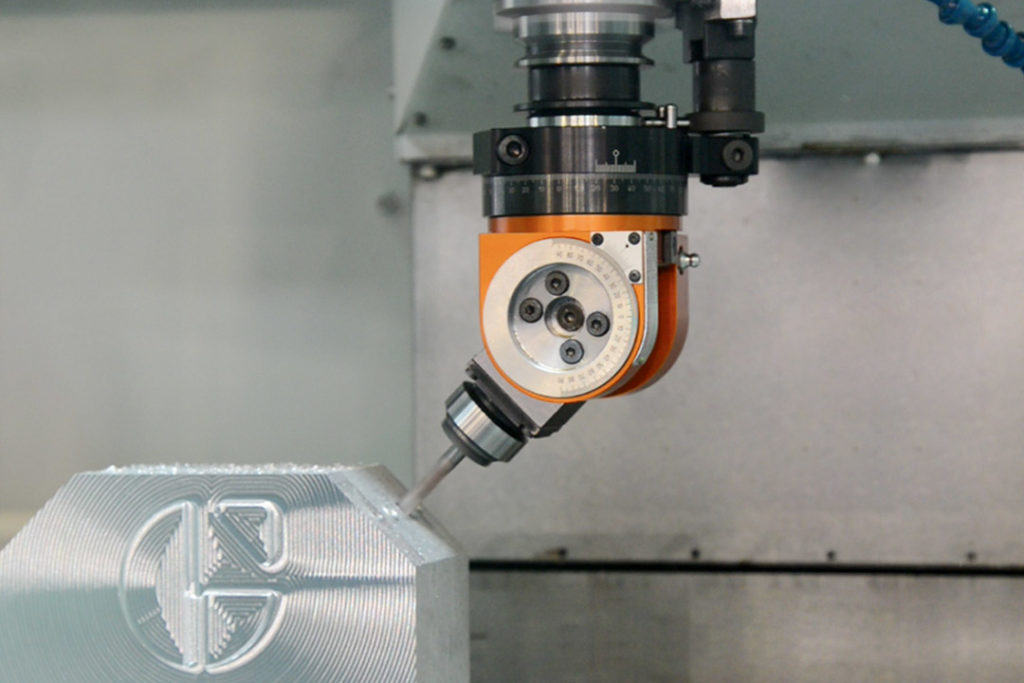
Let’s say you’re machining a mold with a complex design—maybe it’s got a bunch of intricate curves and hard-to-reach corners. With a regular tool, you might have to move the workpiece around multiple times to reach all those spots. But with an adjustable angle head, you can just change the angle of the tool to reach those tricky spots without moving the workpiece.
Or maybe you’re making a mold for a large piece, but there’s a small, detailed area that needs precise machining. Again, the adjustable angle head comes to the rescue. It can be positioned just right to work on that small area without affecting the rest of the piece. It’s a bit like using a small spatula to spread frosting on a tiny corner of your cake without messing up the rest of it.
3. Slim Angle Heads
Ever tried to reach into a narrow, hard-to-reach space with a regular tool? It’s not the easiest task. Even the most advanced 5-axis CNC machining center will give up on you. Enter slim angle heads.
90º Slim angle heads are designed just for that—they have a thin, compact design that lets them access those tight spaces. It’s like when you want to tighten that screw but there isn’t enough space to go at it head on with a regular screwdriver. That’s when you start looking for that right angle screwdriver to save the day.
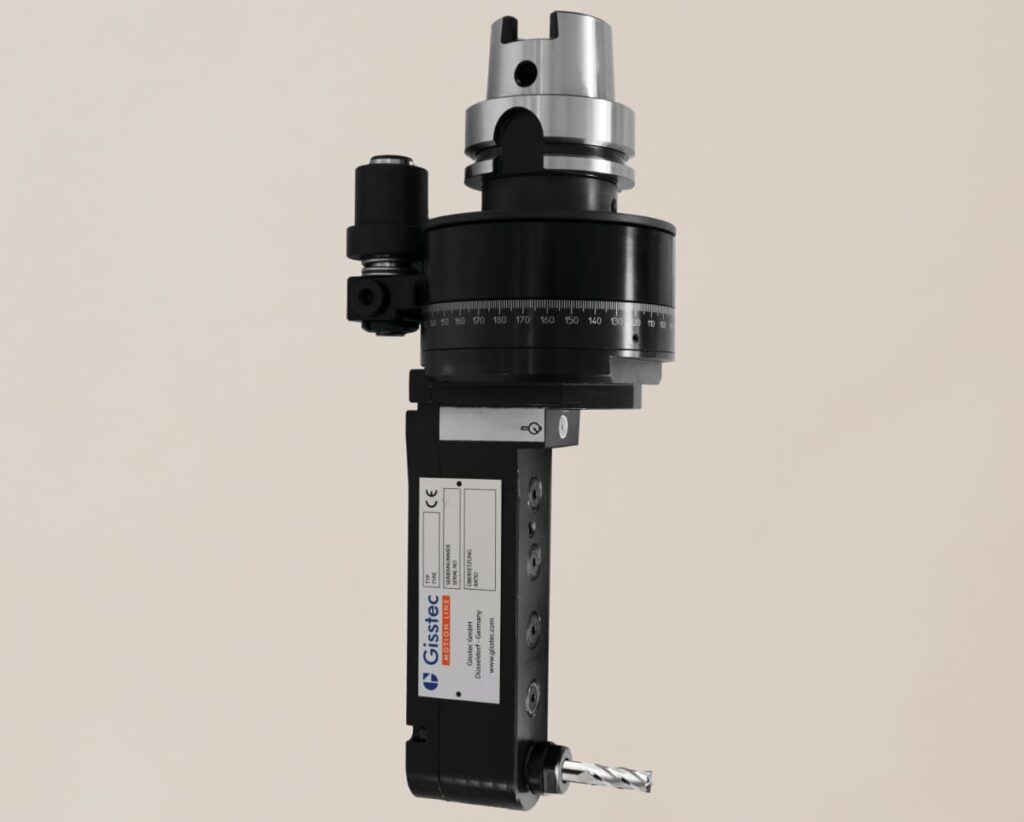
In industries like mold and die making and aerospace, where drilling, tapping or detailed milling inside intricate cavities is needed, slim angle heads come into their own.
These slim angle heads are used in the aerospace industry because aircraft components often require detailed work in confined spaces. Parts such as turbine blades, engine casings, and elements of the landing gear frequently have complex geometries or small features that require precise machining.
Let’s consider an engine casing. This component may also contain small features or holes that need precise machining. With a slim angle head, these spaces become accessible, ensuring each feature is crafted to the exact specifications.
4. Double Output Angle Heads
When it comes to mass production, speed is key. Double output angle heads speed things up by having two output spindles on opposing sides. This comes in handy when working on larger workpieces that have operations on either side.
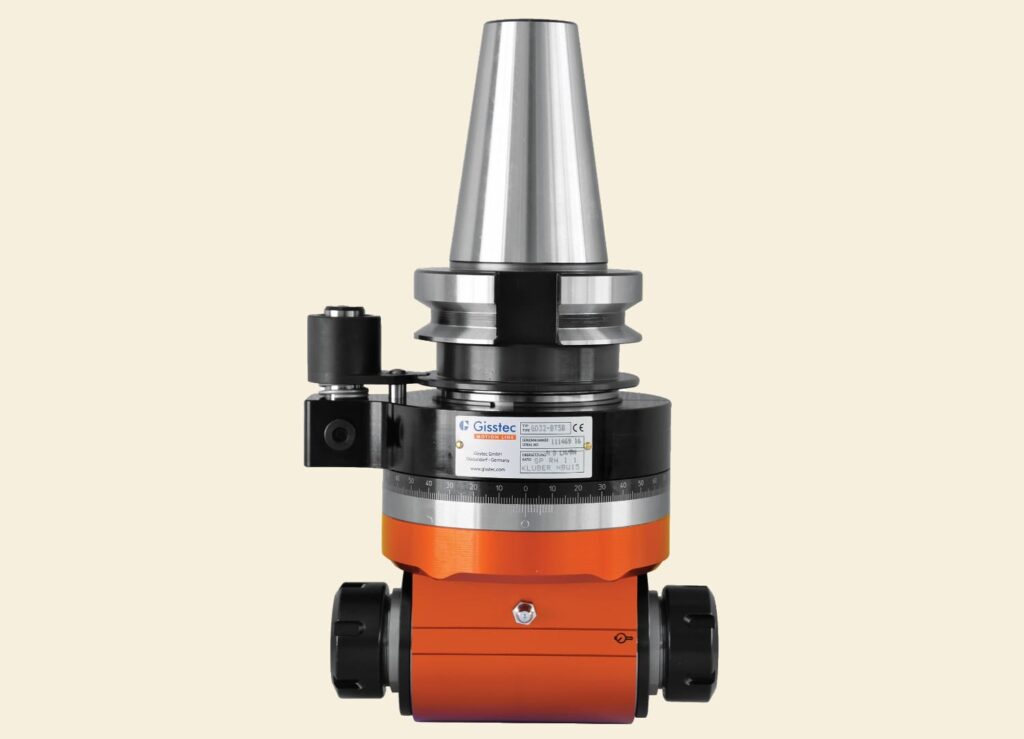
A double output angle head takes care of it without having to change the tool for the second operation. That streamlines the process and shortens the cycle time.
5. Heavy-Duty Angle Heads
Just like it sounds, heavy-duty angle heads are the heavy lifters of the bunch. They’re built to take on high loads and forces. This makes them perfect for big jobs involving a lot of milling, drilling, or tapping, removing considerably more material than its lighter counterparts.
These heads have heavy duty conical bearings that are optimal for withstanding high forces and reducing vibrations. Think of shipbuilding or construction, where the pieces are large and the work is extensive—that’s where these angle heads shine.
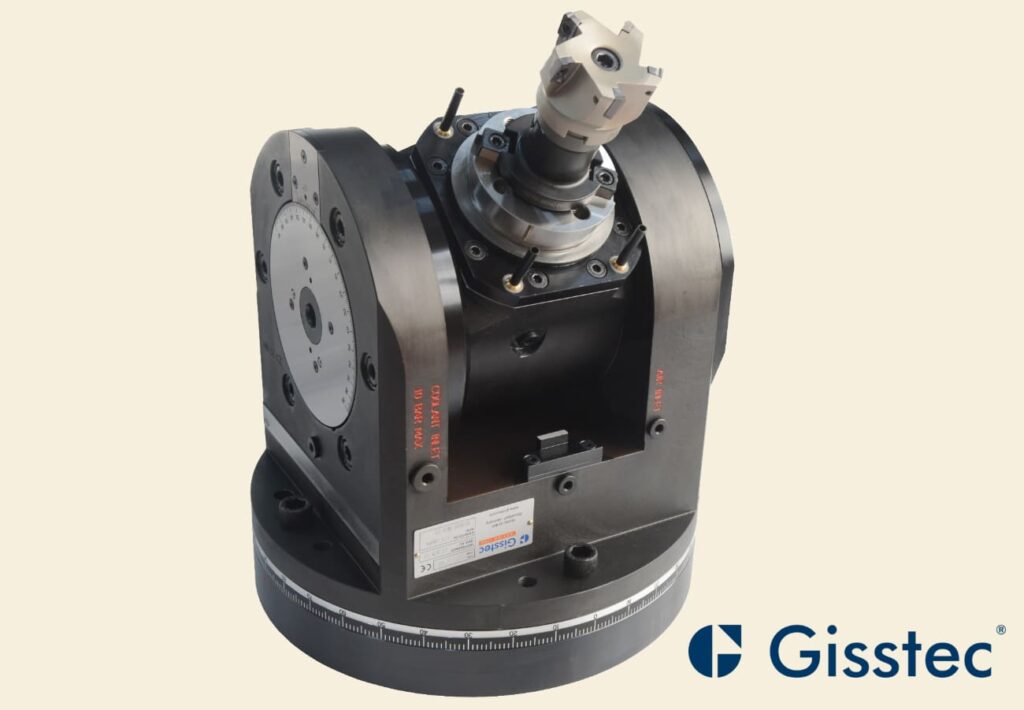
They also accelerate the job of emptying material inside a large mold in moldmaking industry, which can be a very time-consuming operation.
When you’re looking to remove a lot of material, drill large holes, tap big threads, this is your go-to angle head.
6. Modular Angle Heads
Imagine if you could mix and match parts of your angle head to suit different jobs. That’s precisely what modular angle heads offer.
Their design lets you swap out different components depending on the job at hand. It’s a versatile choice that can save a lot of time and resources when dealing with diverse operations on a single workpiece.
It’s also an excellent way of swapping preset cutting tools quickly as a quick-change tool. This reduces the down-time of the machine used for adjusting the cutting tool.
Angle Heads and CNC Machining: How They’re Used in Different Industries
CNC (Computer Numerical Control) machining centers have become more versatile thanks to the addition of angle heads. These handy tools change the direction of the spindle, which lets us do work on multiple sides and axes without needing to move the piece.
Now, we’ll be taking a look at how angle heads are used in various industries.
- Automotive Parts and Perpendicular Operations
Right angle heads are great for machining the sides of parts without having to flip them around. In the car industry, they’re often used for drilling and tapping operations on parts like engine blocks, gearbox housings, and suspension mounts.
- Aerospace Parts with Hard-to-Reach Spots
When making airplane parts, accuracy is key, and often the parts have complex shapes. That’s where adjustable angle heads come in—they can be set at any angle, which helps a lot in this industry. Slim angle heads come to rescue when you need to drill that oil passage hole inside a narrow bore with little clearance.
- Oil & Gas Parts and Deep Hole Drilling
Drilling deep holes into parts can be tricky, especially when the design of the part doesn’t give you much room to work with. That’s where long-reach angle heads are useful. They’re used in the oil and gas industry to drill precise holes in parts like downhole drilling tools, fracking equipment, and oilfield valves.
- Electronics Components Production
When making electronics parts in large volumes, speed and efficiency are essential. Multi-spindle angle heads can do multiple operations at the same time, like drilling and tapping. This helps speed up production, especially for things like consumer electronics casings or connectors.
- Molds, Dies, and Detailing
When you’re making molds and dies, often you have to work in tight, intricate spaces. That’s where slim-bodied angle heads come in handy. They can reach into these small areas and do precise milling operations.
- Jewelry and Art Pieces
For detailed work, like engraving on precious metals or custom art pieces, adjustable angle heads are the way to go. They can handle detailed work on irregular surfaces, ensuring high-quality results.
- Construction and Shipbuilding
For bigger jobs like construction and shipbuilding, you need large-sized angle heads that have a long reach. These heads make it easier to work on big surfaces like beams, hull plates, and large structural sections. They help cut down on the number of times you need to change the setup, which makes things more efficient.
- Medical Implants and Tools
In the medical industry, you need high precision when making things like implants and surgical tools. Adjustable angle heads are used here as well because they can handle the complex operations that are often needed.
Conclusion
As you can see, angle heads have a wide range of uses across different industries. Whether it’s a right angle head for side work, a slim angle head for narrow spaces, or a double output angle head for fast, high-volume jobs, each one has a part to play.
Knowing what each one can do helps you pick the right tool for your job, making your machining processes more efficient and hassle-free.