Broaching on CNC Lathes and Machining Centers
Broaching (Slotting) is a machining process in which a keyway or a profile is created by cutting movements on the Z-axis. The cutting depth is determined with movements of the X-axis. With the working stroke on the Z-axis, material is removed depending on the cutting depth. The return movement is an idle stroke where no material is removed because there is only one cutting direction.
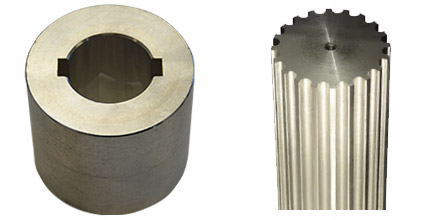
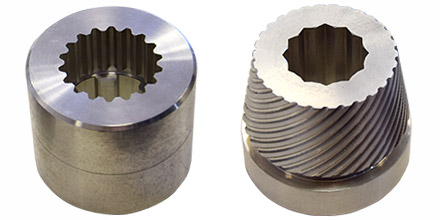
Broaching operations can be done on CNC milling and lathes as well as on broaching machines, whereby most CNC applications occur on lathes, since the workpiece can be finished without re-clamping. The C-axis is required for polygon profiles such as square, hexagonal, serrations and splined shafts. To open a single keyway, only the Z and X axes are usually sufficient. It is important that the lathe’s chuck can be locked, as the chuck must remain fixed while the keyway is being machined.
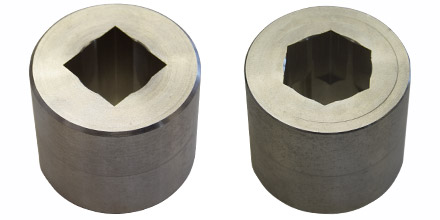
Static and Live Broaching Tools
There are static as well as driven tool solutions. The right choice depends primarily on the number of keyways / edges / teeth and workpieces per month. With a smaller number of workpieces up to around a few thousand pieces per month, the static slotting tools are very cost-effective. However, if the number of pieces is over several thousand per month, a live broaching tool is faster and economically the better solution.
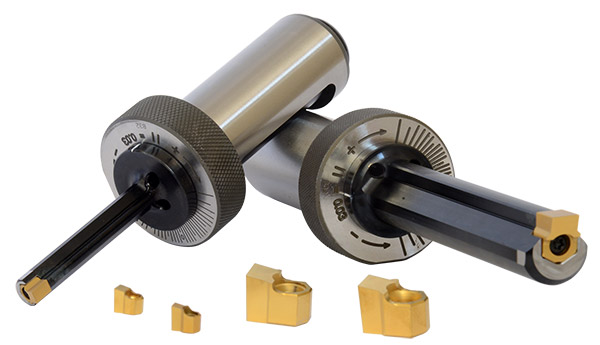
Static broaching solutions, which are widely used, consist of broaching (slotting) tools with a cylindrical clamping option and inserts in various geometries, sizes and tolerances. This technique has two components: the insert and the insert holder. The insert is attached to the insert holder with a screw. The insert holder, usually with a shaft diameter of 25 mm or 32 mm, is then clamped to a boring bar holder or a VDI boring bar holder with a corresponding diameter on the CNC lathe. For use on machining centers, the holder can be clamped with any tool holder with a cylindrical holder, such as a collet chuck or Weldon holder which you can easily supply from your local vendor.
By pushing the insert into the workpiece, the keyway is machined step by step. The cutting speed and the cutting depth must be set depending on the workpiece material. Experience shows here that catalog values mostly only serve as approximate values and that values adapted to various factors on site (room temperature, machine type, machine condition, workpiece quality, coolant, etc.) can produce optimal machining results.
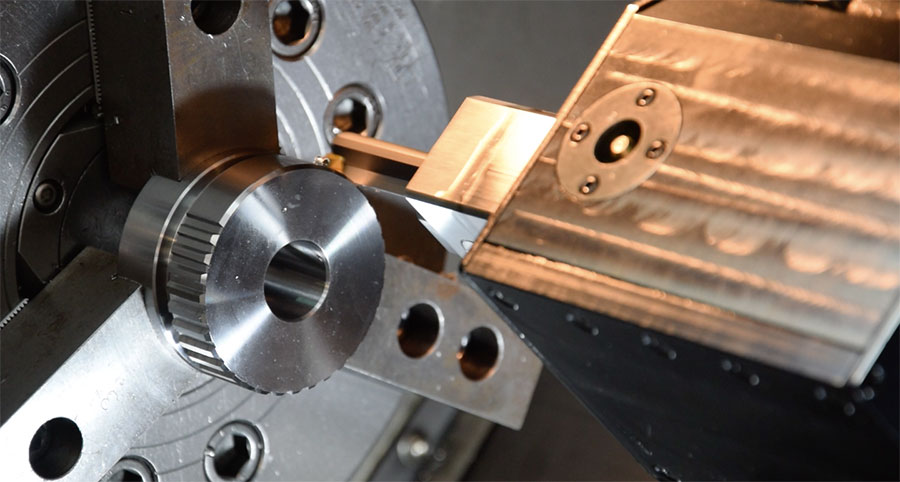
The question that often arises here is whether broaching does not place too much stress on the turret or spindle of the CNC machine. The load that is exerted on the CNC lathe or machining center is comparable to that of a drilling operation. Larger sizes can be machined in two steps first using a smaller insert, then the actual size.
A Y-axis is not necessary for applications on lathes. However, if the lathe does not have a Y-axis, an eccentric bushing is necessary to correct the errors on the theoretical Y-axis of the turret. Over time, there is usually a play in the Y-axis on lathes and so that the grooves are exactly in the middle, this error must be corrected with an eccentric bushing. The C-axis is absolutely necessary for square, hexagonal and gear machining, as all edges or teeth are machined individually.
Comparison of static broaching tools vs live broaching tools:
Static Broaching Tool | Live Broaching Tool | |
Speed | ✖ | ✔ |
No Load on the turret | ✖ | ✔ |
Efficient with higher quantities | ✖ | ✔ |
Efficient with lower quantities | ✔ | ✖ |
Usage without C-Axis | ✔ | ✖ |
Machining length over 65mm | ✔ | ✖ |
Usage on machining centers | ✔ | ✖ |
Keyway, square, hexagon and spline profile machining | ✔ | ✔ |
Live broaching tools are worthwhile for large quantities and provide the following advantages in the long term:
- Cost-efficient production of different geometries
- Resource-saving production and protection of the lathe turret
- Low investment costs compared to purchasing a separate broaching machine
- Fast processing. Up to 400-800 strokes per minute
Example application of the live broaching tool on a lathe with C-axis
Slot Broaching or Rotary Broaching?
For internal square, internal hexagon and internal gear machining, an alternative method is the rotary broaching process. Rotating broaching tools are relatively fast because the entire profile is machined at once and not all edges individually, as is the case with slot broaching.
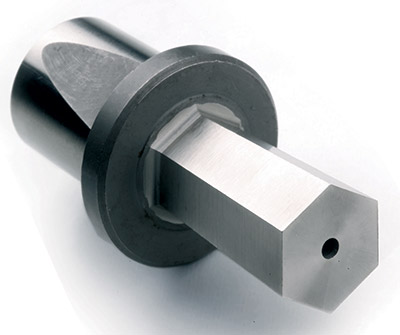
Broaching tools can also be used flexibly on lathes and machining centers. Since processing only has to take place in one pass, the stress on the machine is very high. The machine can often come to a standstill, especially with larger diameters. Process reliability is therefore not guaranteed, especially with larger diameters and materials with higher hardness levels.
With broaching tools, machining can be done in as many passes as necessary. This guarantees process reliability, as the machining parameters can be adjusted depending on the material and profile size.
Comparison: Slot Broaching vs Rotary Broaching
Slot Broaching | Rotary Broaching | |
Process reliability | ✔ | ✖ |
Less load on the machine tool | ✔ | ✖ |
Machining in multiple passes | ✔ | ✖ |
Relatively lower price | ✔ | ✖ |
Machining length over 70mm | ✔ | ✖ |
Machining diameter over 20mm | ✔ | ✖ |
High precision | ✔ | ✖ |
Keyway profile | ✔ | ✖ |
Square, Hexagon, Spline profile | ✔ | ✔ |
Usage on CNC lathe and machining centers | ✔ | ✔ |
Speed | ✖ | ✔ |
Open Polygonal profiles without C-Axis | ✖ | ✔ |
What should you consider when selecting inserts and insert holders?
There are no standard interfaces for inserts and insert holders. This is why vendors of broaching tools usually have a system with their own interfaces and the inserts are usually not interchangeable.
One of the most important technical points to consider when it comes to inserts is the material inserts are made of. Carbide is not suitable for broaching because its low breakage strength does not guarantee process reliability. You can make 100 keyways with a carbide insert, but the edges might break off after a few machining operations. In addition, the surface quality of your keyway might start deteriorating as early as after opening a dozen keyways.
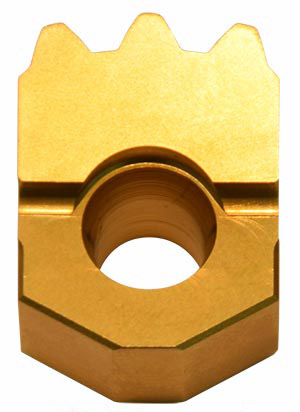
In the manufacture of inserts, preference must be given to materials with high wear resistance and high compressive strength, e.g. powder metallurgical HSS alloys with resistant elements. Inserts made of suitable HSS alloys have a longer life due to the wear resistance and offer much greater process reliability thanks to the high pressure resistance.
With a TIN coating, the wear resistance and life of inserts can be increased. The geometry of the panels is also an important technical point that influences the surface quality, among other things. TiAlN coating may be prefered when machining harder materials.
Comparison: Sintered HSS-Alloy Insert vs Carbide Insert for Broaching
Sintered HSS-Alloy | Carbide | |
Process Reliability | ✔ | ✖ |
Wear Resistance | ✔ | ✖ |
Pressure Resistance | ✔ | ✖ |
Useful Life | ✔ | ✖ |
Constant Surface Quality | ✔ | ✖ |
Resharpening possibility | ✔ | ✔ |
Relatively lower price | ✖ | ✔ |
For the commercial aspects, particular attention should be paid to the size, tolerance and availability selection. If there are several common tolerances to choose from and are available as catalog goods, the procurement costs are lower in contrast to special plates on request. When machining keyways, tolerances H7, JS9, P6 and C11 are the most common.
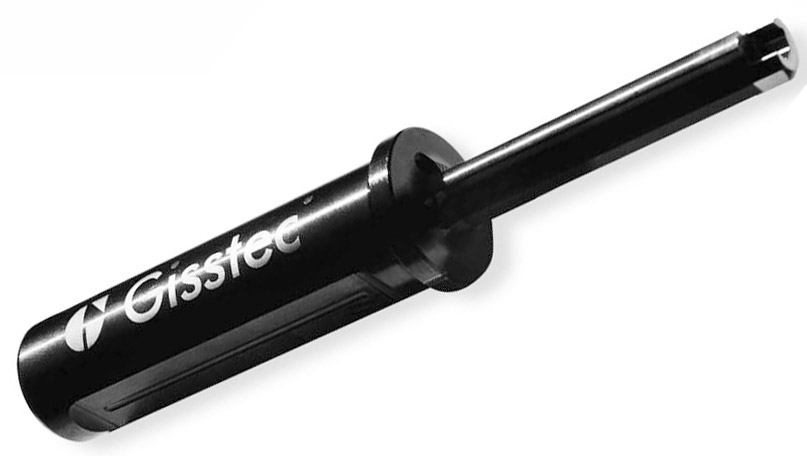
With insert holders, stability is of the utmost importance, as better stability for a longer service life of the inserts and better surface quality. With the holder, a longer shaft contributes to the stability, with a larger contact surface and, if necessary, fastening with two screws instead of one screw. A continuous substructure behind the insert seat ensures vibration damping and thus also increases the stability of the holder. Short insert seat protection must be avoided for optimal surface and service life of the insert.
Coolant supply through the holder ensures removal of the chips, a better surface and protection of the cutting edge.