In industries as diverse as aerospace, aviation, machinery, automative and gear-making, the quest for high precision and efficiency never stops. From jet engine components to gear assemblies, manufacturing processes are evolving to decrease cycle times, increase automation all the while keeping to the strict quality standards.
One such development is the live broaching unit—a compact driven tool that can transform a standard lathe with a C-axis into a versatile keyway-broaching powerhouse.
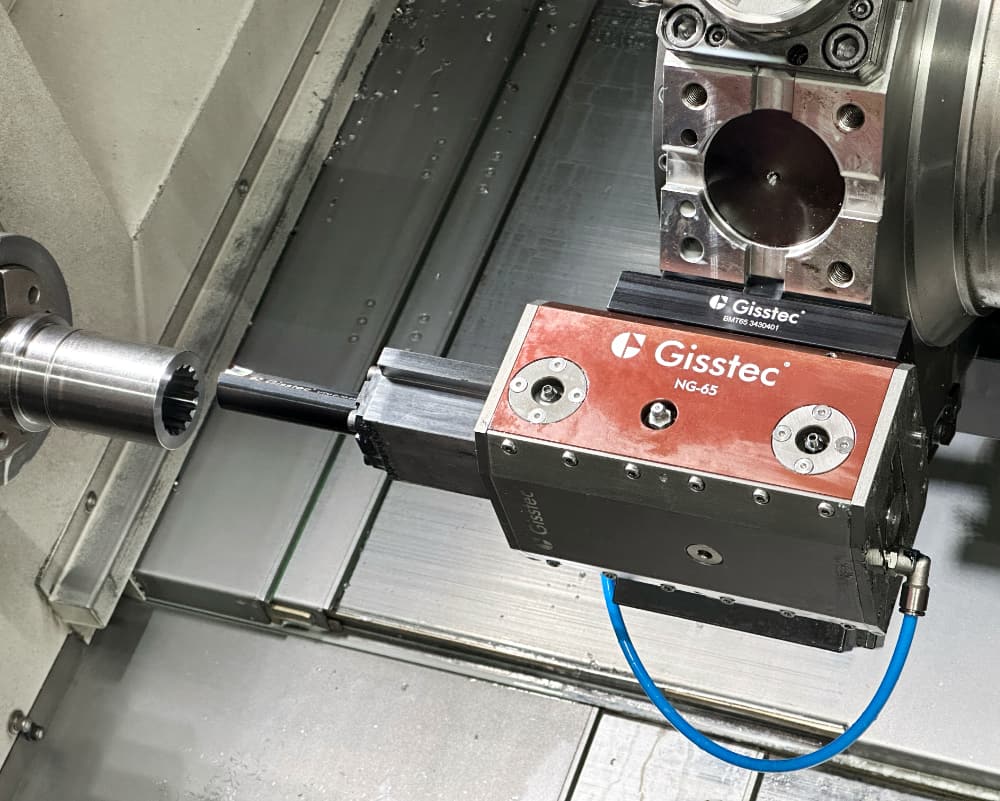
If your operation regularly needs precise internal keyways or spline profiles, this broaching technology could be a pivotal addition to your manufacturing lineup.
Below, we explore how a live broaching unit stacks up against traditional broaching machines and why it’s increasingly becoming the method of choice in demanding manufacturing environments.
Quick Refresher: What Is Keyway Broaching?
Let’s start with the fundamentals. “Broaching” is a material-removal process most commonly associated with cutting keyways. A keyway is a slot, typically inside a gear or rotor, designed to accommodate a “key” that locks onto a shaft. This prevents slippage and provides the robust connection needed for transferring torque — crucial in applications like aircraft engines, power turbines, and industrial gearboxes.
The classic approach to cutting these slots involves a long, multi-tooth keyway broach. During a single pass, each successive tooth removes material until the keyway is fully formed.
Dedicated broaching machines have long been the standard for this operation—especially in high-volume manufacturing. However, they come with specific drawbacks that have spurred many organizations to seek more flexible solutions.
Some companies without a dedicated linear broaching machine or a live broaching tool use broaching services from contract manufacturers which offer tailored solutions to meet specific client needs.
Broaching Machines and Processes
Broaching machines are specialized machine tools designed to perform the cutting process, which involves broaching precise shapes or profiles into workpieces. There are several types of broaching machines, each tailored to specific applications and varying in their mechanism of operation. The most common types include vertical and horizontal broaching machines.
Vertical broaching machines are ideal for applications requiring high precision and are often used for internal broaching tasks. On the other hand, horizontal broaching machines are designed for surface broaching and are typically used for larger workpieces that require extensive material removal.
By understanding the specific advantages and applications of each type of broaching machine, manufacturers can select the most suitable equipment for their needs, ensuring optimal efficiency and precision in their machining processes.
The Traditional Path: Dedicated Vertical Broaching Machines
Single-Purpose Operation
Conventional broaching machines are engineered with one function in mind: broaching. If your line is running large batches of identical parts a dedicated machine may still be a worthwhile choice.
But in modern manufacturing, variety is the new norm. When your product mix changes frequently or you need to produce parts of varying sizes and shapes, moving back and forth between a lathe (for turning, boring, or milling) and a separate broaching machine can become time-consuming. Each part has to be re-fixtured and realigned, introducing more opportunities for dimensional inaccuracies.
High Cost and Maintenance
Industrial broaching equipment is not just large in physical scale; it often comes with a hefty price tag and ongoing maintenance requirements.
In broaching operations, both pull and push methods are employed, each suited to specific applications.
Pull Broaching
Pull broaching, where the broach is drawn through the workpiece, is generally more prevalent, especially for internal broaching tasks. This method allows for longer broaches and is capable of handling more substantial cuts with higher precision.
Pull broaching is commonly utilized in horizontal broaching machines, which are often used for internal broaching of small to medium-sized and heavy workpieces.
Push Broaching
Push broaching involves pushing the broach through or over the workpiece. This technique is typically applied to shorter workpieces or those requiring less material removal, as push broaches are subjected to compressive loads and are made shorter in length to avoid buckling.
Push broaching is commonly used on broaching presses and is suitable for sizing holes and cutting keyways.
Specialized repairs, large-scale hydraulic or mechanical components, and the constant wear on multi-tooth broaches all factor into the total cost of ownership. And multi-tooth broaches are notoriously unforgiving—if a single tooth breaks or chips, the entire broach may need replacing.
Limited to Through Holes
An important limitation for many broaching machines is that they can typically only broach through holes. In aerospace and aviation applications especially, blind holes are often part of complex component designs.
Traditional machines that rely on pulling or pushing a broach through the entire workpiece generally aren’t equipped to handle those partial-depth requirements.
The New Approach: Live Broaching Units on a Lathe
Compact and Flexible
A live broaching unit is a specialized driven tool for linear broaching that mounts directly onto a CNC lathe’s turret or tool post. It’s compact, easy to mount, and doesn’t require the additional floor space of a standalone broaching machine.
This is particularly relevant in high-volume manufacturing lines where every square foot of space counts—or in advanced facilities where multiple processes must be consolidated to shorten production times.
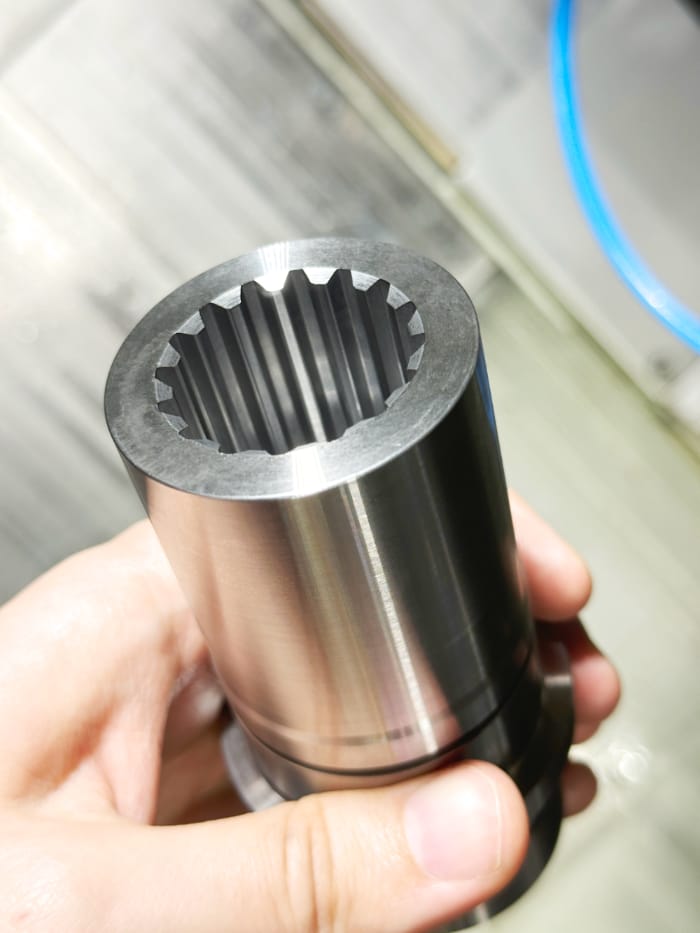
Seamless Workflow
One of the most compelling advantages is the ability to perform everything—turning, boring, drilling, and broaching—on the same machine.
This means fewer setups, reduced part handling, and minimal risk of misalignment. Whether you’re machining precision engine components for aircraft or specialized gears for heavy equipment, having all your operations in one place can significantly streamline production.
Cost-Effective Insert-Based Broaching Tools
Where traditional machines rely on large, multi-tooth broaches, live broaching units generally use single-tooth or indexable inserts.
These inserts are economical, can be swapped out easily when worn or chipped, and allow for quick adaptation to different keyway sizes or shapes. Broach tools are versatile and have specific applications in machining processes, making them essential for achieving accurate finishes and efficient material removal across various materials like alloy steel, cast iron, aluminum, bronze.
If you’re producing diverse runs—like different gear diameters or varied aerospace components—this approach can be a major money-saver. The days of scrapping an entire multi-tooth broach because one tooth is damaged are over.
Blind Hole Capability
Unlike most dedicated broaching setups, a live broaching unit can cut keyways into blind holes. All you need is a small relief groove to allow chip evacuation at the profile’s end, and you’re set.
This opens the door for more intricate part designs common in turbines, pump systems, and rotor assemblies, where partial-depth keyways are often critical for performance.
Simplifying Complex Designs
Engineers have historically been forced to design around the constraints of through-hole machining, sometimes resulting in overly complex or hard-to-manufacture parts.
Now, with advancements such as live broaching units and improved tooling technology, designs can be approached more freely, allowing blind holes and partial length keyways and involute spline profiles to be incorporated without compromising manufacturability.
This flexibility not only simplifies the production process but also opens the door for innovative component designs that were previously impractical.
Advantages Across Industries
Faster Turnaround with Reduced Handling
Every time a part is transferred from one machine to another, there’s a chance for error or damage. In aerospace or aviation manufacturing, where tolerances can be extremely tight, minimizing re-fixturing is essential. Live broaching keeps the workpiece in the lathe chuck, ensuring consistent alignment and rapid part processing.
Lower Overall Investment
Dedicated broaching machines can command a significant upfront investment, not to mention the operating and maintenance costs.
A live broaching unit, on the other hand, is typically far less expensive and makes use of your existing equipment and infrastructure.
This more flexible setup can be appealing if you’re balancing the purchase of other specialized machinery—like 5-axis CNC mills or advanced inspection systems—needed for cutting-edge aviation or aerospace projects.
Scalable for Large or Small Batches
Some industries—such as gear-making for large-scale construction equipment—might deal with extensive production runs. Others, like custom aerospace component manufacturers, may see smaller, highly specialized batches.
Live broaching units adapt easily to both situations. When you’re producing keyways across various part sizes, simply swap out the inserts as needed. This adaptability keeps machine downtime to a minimum, allowing you to respond quickly to changing production orders.
Integrated Programming and Automation
Modern CNC lathes often come with sophisticated software that can handle complex tool paths, and integrating a broaching operation is typically a straightforward add-on.
The manufacturing process can be automated using the same G-code routines you employ for turning and milling, simplifying training and reducing the risk of human error.
In sectors where process validation and repeatability are paramount—like aerospace—this level of control can significantly improve quality assurance.
Improved Floor Space Utilization
Whether you’re building jet engines or heavy industrial gearboxes, the manufacturing floor is always at a premium. By attaching a broaching unit to your lathe, you avoid having to carve out space for a standalone broaching system.
That’s good news for sprawling factory setups where multiple production lines operate simultaneously, as well as for more constrained facilities that are constantly juggling machine placement.
How About Rotary Braoching?
Rotary broaching is a unique machining process designed to efficiently create precise internal and external profiles by simultaneously rotating both the cutting tool and the workpiece.
This technique is widely used in applications requiring polygonal shapes such as hexagon holes, square holes, or splines, often found in fasteners, gears, and other mechanical components.
How Does Rotary Broaching Work?
In rotary broaching, the cutting tool is mounted at a slight angle (typically 1°) relative to the workpiece axis. As the tool and workpiece rotate, the angled broach applies pressure to cut the desired profile.
The key to this process is the synchronized rotation of the tool and workpiece, which reduces cutting resistance and enables the broach to carve out the profile with precision and minimal stress.
Key Benefits of Rotary Broaching
- Efficiency: It completes the profile in a single pass, significantly reducing cycle times compared to multi-step broaching processes.
- Versatility: The process can be applied to a wide range of materials, including steel, aluminum, and titanium, making it suitable for industries such as aerospace, automotive, and medical devices.
- Compact Setup: Internal broaching and external broaching can be performed on standard CNC lathes, turning machines, machining centers or mills with the appropriate tool holders.
Limitations of Rotary Broaching
While rotary broaching offers numerous advantages, it is not without its limitations:
- High Cutting Forces: The process requires substantial cutting forces, limiting the size and depth of the profiles that can be created. Very deep or large profiles may exceed the capacity of rotary broaching tools. That’s where live broaching tools come in.
- Material Hardness: Extremely hard materials may pose challenges for rotary broaching, as the required cutting forces increase significantly.
- Complex Profiles: While excellent for simple polygonal shapes, rotary broaching is not ideal for creating highly intricate or non-uniform profiles.
Applications of Rotary Broaching
Rotary broaching is a go-to process for a variety of industries and applications :
- Fasteners: Manufacturing hexagonal, square or torx sockets for bolts, screws, and other fasteners.
- Gears and Splines: Producing internal splines or other profiles used in power transmission components.
- Medical Devices: Machining precise internal features in surgical instruments and implants.
Important Considerations Before Making the Switch
Lathe Requirements
Not all lathes are created equal. Your lathe needs to be rigid enough and have sufficient horsepower to handle the forces generated during broaching—especially for larger or tougher materials frequently used in aerospace (think titanium or high-strength steel).
Always consult the manufacturer’s recommended guidelines for spindle power, tool pressure, and cutting speeds.
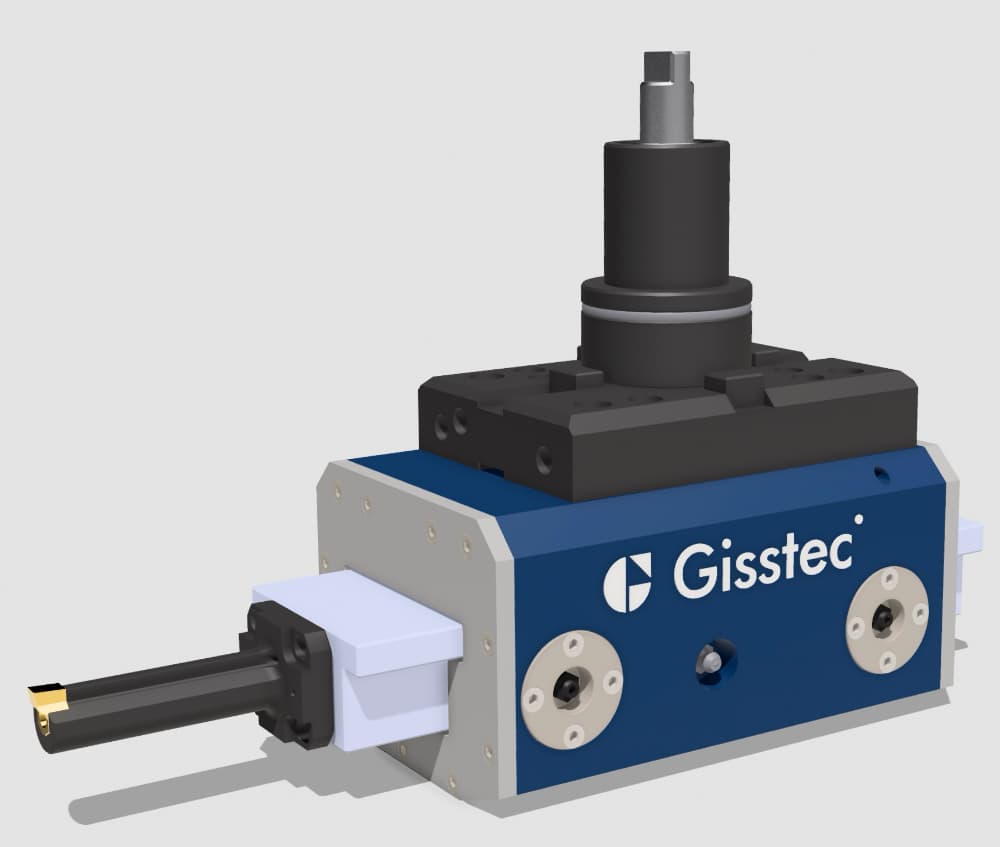
Monitoring Tool Wear
Broaching, like any machining operation, puts stress on cutting edges. If you’re working with exotic aerospace alloys or hardened gear steels, tool wear can accelerate. Regular inspection and routine insert changes will help maintain quality.
Adhering to recommended speeds, feeds, and lubrication protocols also prolongs tool life.
Safety and Training
Proper training is non-negotiable. While attaching and using a live broaching unit isn’t overly complex, it does require a solid understanding of both lathe operations and broaching fundamentals.
Employees should be aware of clearance settings, proper clamping procedures, and safety measures like protective eyewear and guarding.
Conclusion
From aerospace engine shafts to massive gears in heavy machinery, keyways are integral to ensuring reliable power transmission. While traditional broaching machines have served this purpose for decades, the rise of live broaching units is reshaping how companies approach the task.
They’re flexible, cost-effective, and efficient, making it easier than ever to integrate keyway broaching right on the production floor—no additional machine required.
If your organization is grappling with tight deadlines, space constraints, or a diverse product mix, consider a live broaching unit. You’ll save on tooling, speed up production, and open the door to new design possibilities such as blind hole keyways.
Dedicated broaching machines may still hold their ground in certain high-volume or specialized scenarios. But for many operations across aerospace, aviation, machinery, and gear-making, the adaptability and efficiency of live broaching can be a game-changer.
In the high-stakes world of advanced manufacturing—where efficiency, precision, and innovation converge—every competitive edge counts.
By integrating a live broaching unit into your lathe-driven workflow, you can expand your capabilities, reduce overhead, and maintain the high quality your clients demand.
Whether you’re building the next generation of jet engines or large industrial gear trains, live broaching could be the key to elevating your production processes to new heights.
FAQ
1. What is a live broaching unit?
A live broaching unit is a compact, driven tool that attaches to a lathe, transforming it into a keyway-broaching powerhouse. This attachment enables efficient cutting of keyways, involute spline profiles, and other intricate shapes directly on the lathe, eliminating the need for separate broaching machines.
2. How does a live broaching unit work?
Live broaching units use single-tooth or indexable inserts mounted on a lathe’s turret or tool post. The unit applies precise cutting forces to create keyways or splines while the workpiece is held in place. This process reduces setup time and ensures consistent results in a single machine setup.
3. What are the advantages of live broaching units compared to traditional broaching machines?
- Space-saving: Live broaching units eliminate the need for a separate broaching machine.
- Cost-effective tooling: They use replaceable inserts, reducing the cost of tooling compared to multi-tooth broaches.
- Flexibility: They allow for blind hole broaching, enabling complex designs.
- Time efficiency: Operations like turning, boring, and broaching can be performed in one setup, reducing handling and cycle times.
4. Can live broaching units handle blind holes?
Yes, live broaching units can cut keyways into blind holes. By incorporating a small relief groove at the bottom of the hole, chip evacuation is made possible, overcoming the limitations of traditional broaching machines that can only handle through holes.
5. What types of broaching processes are commonly used?
- Pull Broaching: The broach is pulled through the workpiece, ideal for internal broaching with high precision.
- Push Broaching: The broach is pushed through or over the workpiece, suitable for smaller cuts and shallow profiles.
- Rotary Broaching: The tool and workpiece rotate simultaneously, perfect for creating polygonal shapes like hexagons and squares in one pass.
6. What are the limitations of traditional broaching machines?
- They are generally limited to through holes.
- High equipment costs and maintenance needs.
- Limited flexibility for low-volume or highly varied production runs.
- Multi-tooth broaches are expensive and can become unusable if a single tooth is damaged.
7. What are the key benefits of rotary broaching?
Rotary broaching is highly efficient for creating profiles such as hexagons and squares. It completes the profile in a single pass and is versatile enough for a wide range of materials, including steel, aluminum, and titanium. However, it requires substantial cutting forces and is less suitable for large or intricate profiles.
8. How do live broaching units impact manufacturing flexibility?
Live broaching units allow engineers to design freely without being constrained by the limitations of through-hole broaching. Features like blind holes and partial-depth keyways can now be incorporated without compromising manufacturability, enabling more innovative and cost-effective designs.
9. What industries benefit most from live broaching units?
Industries such as aerospace, aviation, machinery, gear-making, and medical device manufacturing benefit from live broaching units due to their ability to handle precision components efficiently while maintaining high quality.
10. What factors should be considered before using a live broaching unit?
- Lathe capability: Ensure your lathe is rigid enough and has sufficient power for broaching.
- Tool wear: Regularly inspect and replace inserts to maintain quality.
- Training: Operators must understand the process and safety measures for successful implementation.
11. Why are live broaching units more cost-effective?
Live broaching units use affordable, replaceable inserts instead of expensive multi-tooth broaches. This reduces tooling costs significantly, especially for varied production runs or applications requiring frequent insert changes.
12. What are the best applications for live broaching units?
Live broaching units are ideal for:
- Keyways in blind and through holes.
- Internal spline profiles for gear systems.
- Aerospace and automotive components requiring tight tolerances and complex features.
13. Can rotary broaching be performed on a standard CNC lathe?
Yes, rotary broaching can be performed on standard CNC lathes or mills equipped with the appropriate tool holders, making it a versatile option for creating polygonal shapes in fasteners, gears, and other components.
14. How do live broaching units improve production efficiency?
By combining turning, boring, and broaching in a single machine setup, live broaching units reduce part handling, minimize re-fixturing, and speed up production cycles while maintaining precision.
15. How do live broaching units simplify complex designs?
Engineers no longer need to design around through-hole constraints. Live broaching units allow for the seamless inclusion of blind holes, partial-depth keyways, and intricate profiles, making previously challenging designs more feasible to manufacture.
Keywords: Live broaching unit, driven broaching tool, push broaching, pull broaching, rotary broaching, continuous broaching